Ken Garrett explains target costing and life-cycle costing, and gives examples as to how and when you would use these costing techniques
Target costing and life-cycle costing can be regarded as relatively modern advances in management accounting, so it is worth first looking at the approach taken by conventional costing.
Typically, conventional costing attempts to work out the cost of producing an item incorporating the costs of resources that are currently used or consumed. Therefore, for each unit made the classical variable costs of material, direct labour and variable overheads are included (the total of these is the marginal cost of production), together with a share of the fixed production costs. The fixed production costs can be included using a conventional overhead absorption rate (absorption costing (AC)) or they can be accounted for using activity-based costing (ABC). ABC is more complex but almost certainly more accurate. However, whether conventional overhead treatment or ABC is used the overheads incorporated are usually based on the budgeted overheads for the current period.
Once the total absorption cost of units has been calculated, a mark-up (or gross profit percentage) is used to determine the selling price and the profit per unit. The mark-up is chosen so that if the budgeted sales are achieved, the organisation should make a profit.
There are two flaws in this approach:
- The product’s price is based on its cost, but no‑one might want to buy at that price. The product might incorporate features which customers do not value and therefore do not want to pay for, and competitors’ products might be cheaper, or at least offer better value for money. This flaw is addressed by target costing.
- The costs incorporated are the current costs only. They are the marginal costs plus a share of the fixed costs for the current accounting period. There may be other important costs which are not part of these categories, but without which the goods could not have been made. Examples include the research and development costs and any close down costs incurred at the end of the product’s life. Why have these costs been excluded, particularly when selling prices have to be high enough to ensure that the product makes an overall profit for the company. To make a profit, total revenue must exceed total costs in the long-term. This flaw is addressed by life-cycle costing.
Target costing
Target costing is very much a marketing approach to costing. The Chartered Institute of Marketing defines marketing as:
‘The management process responsible for identifying, anticipating and satisfying customer requirements profitably.’
In marketing, customers rule, and marketing departments attempt to find answers to the following questions:
- Are customers homogeneous or can we identify different segments within the market?
- What features does each market segment want in the product?
- What price are customers willing to pay?
- To what competitor products or services are customers comparing ours?
- How will we advertise and distribute our products? (There are costs associated with those activities too)
Marketing says that there is no point in management, engineers and accountants sitting in darkened rooms dreaming up products, putting them into production, adding on, say 50% for mark-up then hoping those products sell. At best this is corporate arrogance; at worst it is corporate suicide.
Note that marketing is not a passive approach, and management cannot simply rely on customers volunteering their ideas. Management should anticipate customer requirements, perhaps by developing prototypes and using other market research techniques.
Therefore really important information relating to a new product is:
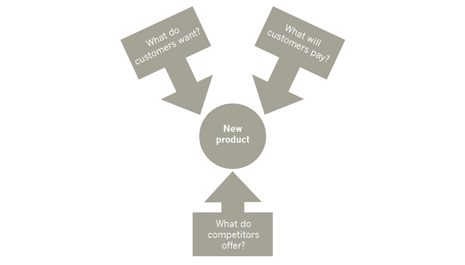
Of course, there will probably be a range of products and prices, but the company cannot dictate to the market, customers or competitors. There are powerful constraints on the product and its price and the company has to make the required product, sell it at an acceptable and competitive price and, at the same time, make a profit. If the profit is going to be adequate, the costs have to be sufficiently low. Therefore, instead of starting with the cost and working to the selling price by adding on the expected margin, target costing will start with the selling price of a particular product and work back to the cost by removing the profit element. This means that the company has to find ways of not exceeding that cost.
Example:
If a company normally expects a mark-up on cost of 50% and estimates that a new product will sell successfully at a price of $12, then the maximum cost of production should be $8:
Cost 100% $8 |
+ |
Mark-up |
= |
Selling price |
This is a powerful discipline imposed on the company. The main results are:
- The establishment of multifunctional teams consisting of marketing people, cost accountants, production managers, quality control professionals and others. These teams are vital to the design and manufacturing decisions required to determine the price and feature combinations that are most likely to appeal to potential buyers of products.
- An emphasis on the planning and design stage. This becomes very important to the cost of the product because if something is designed such that it is needlessly expensive to make, it does not matter how efficient the production process is, it will always be a struggle to make satisfactory profits.
Here are some of the decisions, made at the design stage, which can affect the cost of a product:
- the features of the product
- how to avoid ‘over design’
- the number of components needed
- whether the components are standard or specialised
- the complexity of machining and construction
- where the product can be made
- what to make in-house and what to sub-contract
- the quality of the product
- the batch size in which the product can be made
You will see from this list that activity-based costing can also play an important part in target costing. By understanding the cost drivers (cost causers) a company can better control its costs. For example, costs could be driven down by increasing batch size, or reducing the number of components that have to be handled by stores. The concept of value engineering (or value analysis) can be important here. Value engineering aims to reduce costs by identifying those parts of a product or service which do not add value – where ‘value’ is made up of both:
- use value (the ability of the product or service to do what it sets out to do – its function) and
- esteem value (the status that ownership or use confers)
The aim of value engineering is to maximise use and esteem values while reducing costs. For example, if you are selling perfume, the design of its packaging is important. The perfume could be held in a plain glass (or plastic) bottle, and although that would not damage the use value of the product, it would damage the esteem value. The company would be unwise to try to reduce costs by economising too much on packaging. Similarly, if a company is trying to reduce the costs of manufacturing a car, there might be many components that could be satisfactorily replaced by cheaper or simpler ones without damaging either use or esteem values. However, there will be some components that are vital to use value (perhaps elements of the suspension system) and others which endow the product with esteem value (the quality of the paint and the upholstery).
Life-cycle costing
As mentioned above, target costing places great emphasis on controlling costs by good product design and production planning, but those up‑front activities also cause costs. There might be other costs incurred after a product is sold such as warranty costs and plant decommissioning. When seeking to make a profit on a product it is essential that the total revenue arising from the product exceeds total costs, whether these costs are incurred before, during or after the product is produced. This is the concept of life cycle costing, and it is important to realise that target costs can be driven down by attacking any of the costs that relate to any part of a product’s life. The cost phases of a product can be identified as:
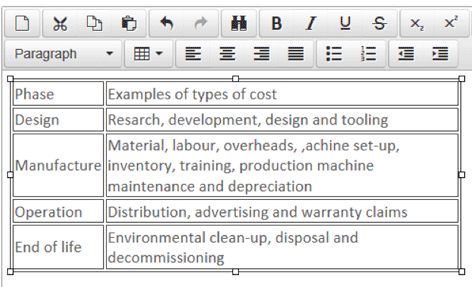
There are four principal lessons to be learned from life-cycle costing:
- All costs should be taken into account when working out the cost of a unit and its profitability.
- Attention to all costs will help to reduce the cost per unit and will help an organisation achieve its target cost.
- Many costs will be linked. For example, more attention to design can reduce manufacturing and warranty costs. More attention to training can machine maintenance costs. More attention to waste disposal during manufacturing can reduce end-of life costs.
- Costs are committed and incurred at very different times. A committed cost is a cost that will be incurred in the future because of decisions that have already been made. Costs are incurred only when a resource is used.
Typically, the following pattern of costs committed and costs incurred is observed:
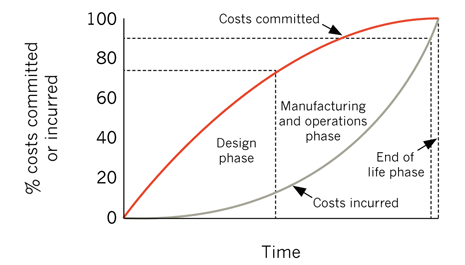
The diagram shows that by the end of the design phase approximately 80% of costs are committed. For example, the design will largely dictate material, labour and machine costs. The company can try to haggle with suppliers over the cost of components but if, for example, the design specifies 10 units of a certain component, negotiating with suppliers is likely to have only a small overall effect on costs. A bigger cost decrease would be obtained if the design had specified only eight units of the component. The design phase locks the company in to most future costs and it this phase which gives the company its greatest opportunities to reduce those costs.
Conventional costing records costs only as they are incurred, but recording those costs is different to controlling those costs and performance management depends on cost control, not cost measurement.
A numerical example of target and life-cycle costing
A company is planning a new product. Market research information suggests that the product should sell 10,000 units at $21.00/unit. The company seeks to make a mark-up of 40% product cost. It is estimated that the lifetime costs of the product will be as follows:
- Design and development costs $50,000
- Manufacturing costs $10/unit
- End of life costs $20,000
The company estimates that if it were to spend an additional £15,000 on design, manufacturing costs/unit could be reduced.
Required:
(a) What is the target cost of the product?
(b) What is the original life-cycle cost per unit and is the product worth making on that basis?
(c) If the additional amount were spent on design, what is the maximum manufacturing cost per unit that could be tolerated if the company is to earn its required mark-up?
Solution:
The target cost of the product can be calculated as follows:
(a)
Cost 100% $15 |
+ |
Mark-up |
= |
Selling price |
(b) The original life cycle cost per unit = ($50,000 + (10,000 x $10) + $20,000)/10,000 = $17
This cost/unit is above the target cost per unit, so the product is not worth making.
(c) Maximum total cost per unit = $15. Some of this will be caused by the design and end of life costs:
($50,000 + $15,000 + $20,000)/10,000 = $8.50
Therefore, the maximum manufacturing cost per unit would have to fall from $10 to ($15 – $8.50) = $6.50.
Ken Garrett is a freelance lecturer and author